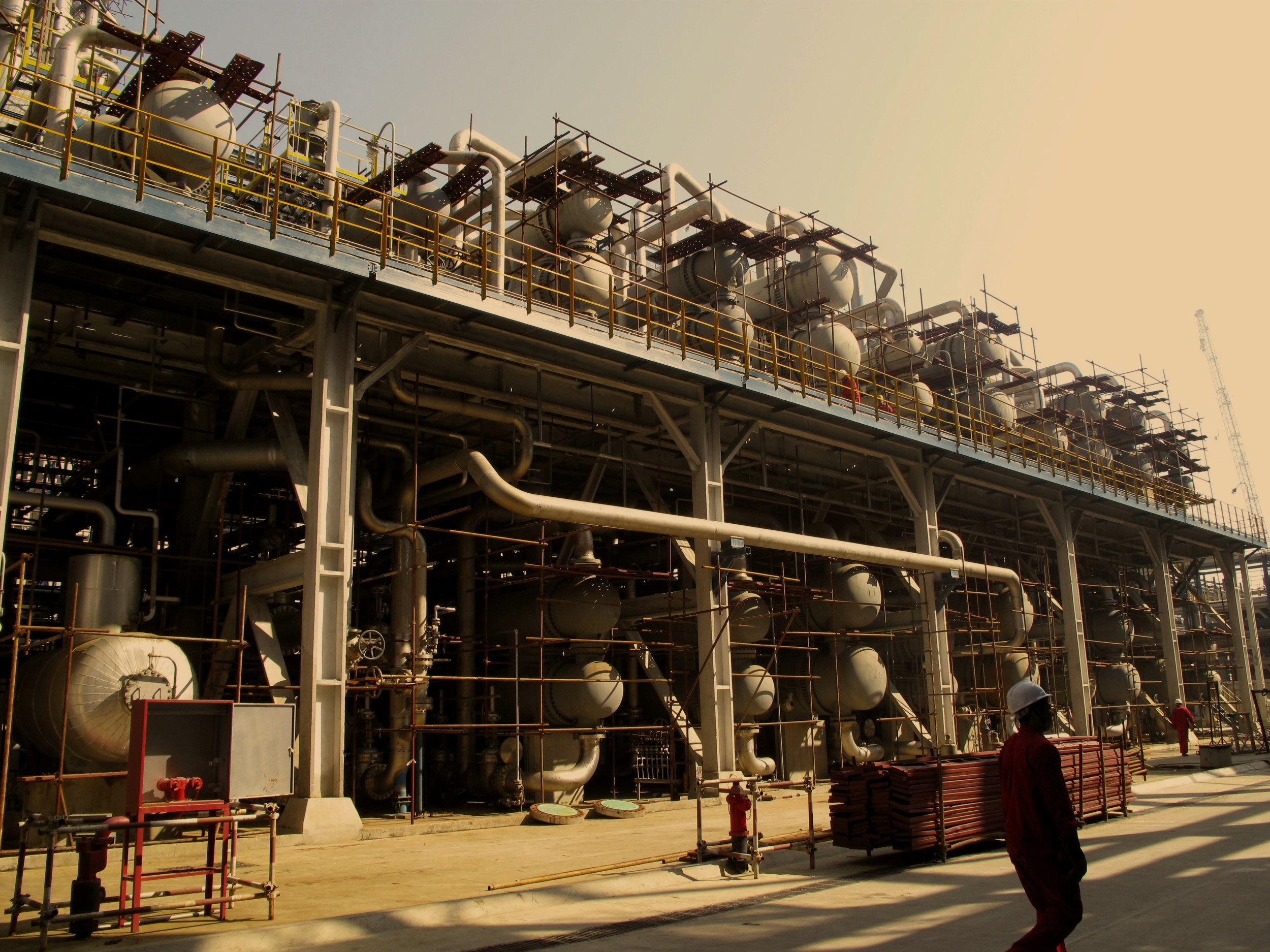
FLUID CATALYTIC CRACKING UNITS
Although we do not service the FCCU reactor-regenerator, Process Consulting Services’ distillation expertise has led to many successful revamp and grassroots projects within the scope of the FCC main fractionator and gas plant. Our projects have included several FCC units with feed rates over 100 Mbpd.
The FCCU main fractionator and gas plant is usually designed by a licensor based on standard design procedures. Often these designs fail to maximize diesel recovery from lower value products. Losing diesel boiling range material to the naphtha, slurry, or HCGO products lowers refinery profitability. Process Consulting Services’ designs target maximum profitability rather than blindly adhering to standard practices.
Revamps can maximize gas plant performance with existing equipment. For example, a revamp may make use of structured packing to reduce fractionator pressure drop. The result is a higher compressor suction pressure that significantly increases gas handling without the need for an expensive compressor replacement. Gas plant C3+ recovery can materially influence overall refinery liquid volume recovery.
For questions about revamps or how to maximize plant performance, call 713-665-7046.
LUBE VACUUM UNITS
Process Consulting Services has performed both revamps and grassroots projects on lube vacuum units, some of which process over 100 Mbpd. Lube vacuum units fractionate atmospheric residue into products for further downstream processing. Optimizing column operating pressure, heater outlet temperature and stripping section performance ensures lube product yields are maximized, which is vital as lube product values can be $60-$80 per barrel higher than vacuum residue. Unlike fuels vacuum towers, lube towers must fractionate the feed to maximize the highest valued products while maintaining quality that allows optimum downstream processing.
Maximizing fractionation efficiency in large diameter packed vacuum columns requires excellent liquid distribution and proper internals designs. At Process Consulting Services all essential process and equipment design is performed in-house, including the design of the column internals. By designing the internals we eliminate the typical pitfall that commonly occurs when mass transfer vendors are forced to cut corners in their proposed equipment design in order to win the job. Our design packages ensure that the equipment is efficient, flexible, and reliable enough to meet our clients’ objectives.

COKING UNITS
Process Consulting Services has completed projects for coking units from the main fractionator through the gas plant, including units operating above 75 Mbpd.
Delayed coker main fractionators and gas plants are often designed by licensors based on standard design procedures. Often these designs fail to maximize diesel recovery from lower value products. Losing diesel boiling range material to the naphtha or HCGO products lowers refinery profitability. Process Consulting Services’ designs target maximum profitability rather than blindly adhering to standard practices.
Revamps can maximize gas plant performance with existing equipment. For example, a revamp may make use of structured packing to reduce fractionator pressure drop. The result is a higher compressor suction pressure that significantly increases gas handling without the need for an expensive compressor replacement. Gas plant C3+ recovery can materially influence overall refinery liquid volume recovery.
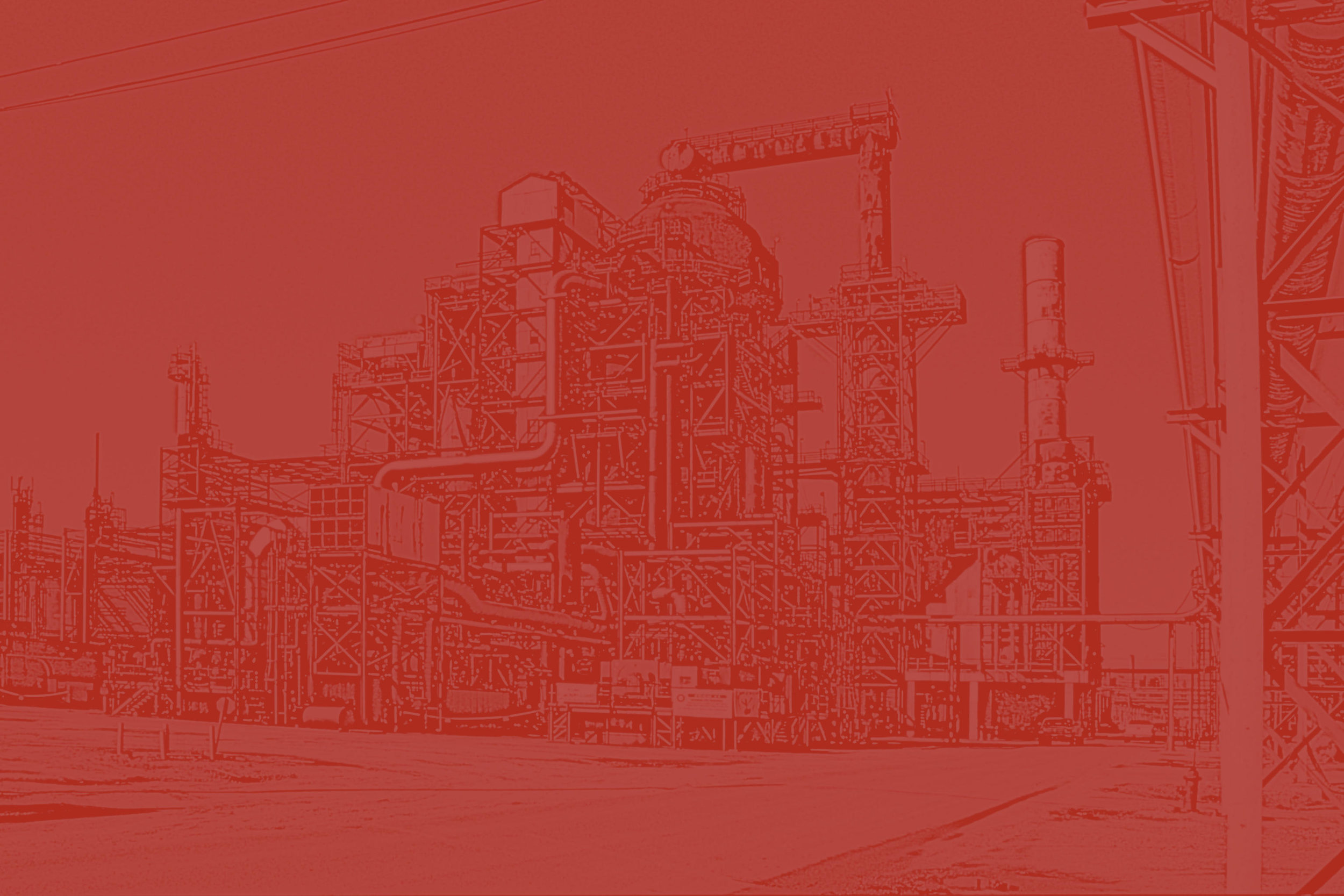
OTHER DISTILLATION PROCESSES
Process Consulting Services has completed revamps and design work around many other distillation-intensive processes. Some of these include aromatics, solvents, and condensate processing. Our deep understanding and application of distillation and engineering fundamentals allows us to produce efficient, flexible, operable, profitable designs for our customers.
Aromatic processing requires special vapor/liquid equilibrium data and equipment design know-how. Solvent processing produces narrow boiling range cuts that must be sharply fractionated due to unique product usage. Often tight sands crudes have to be stabilized or topped to ensure they can be processed through existing refinery crude units and gas plants. Eagle Ford, Bakken, Colorado, West Texas and other tights sands production material cannot be processed in high percentages without loss of capacity. Furthermore, these crudes have some unique contaminants that require special process design considerations.

GENERAL PROCESS EQUIPMENT
Because Process Consulting Services provides all essential equipment design as part of our Process Design Packages, we can also provide equipment design services for large, important equipment such as distillation columns, heaters, heat exchangers and vacuum ejectors. In-house equipment knowledge allows better designs that reduce energy consumption, improve reliability and ultimately increase profitability.
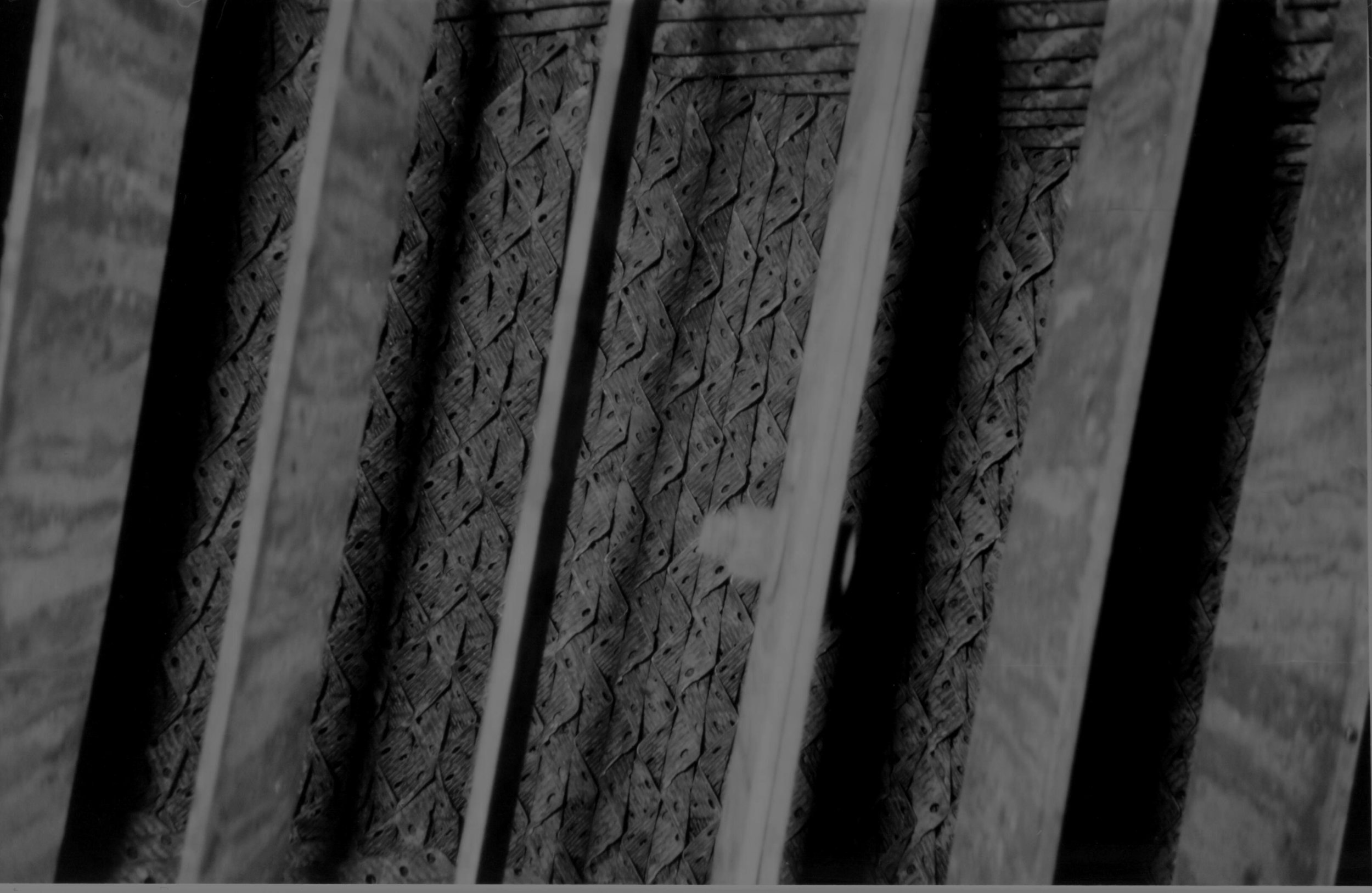